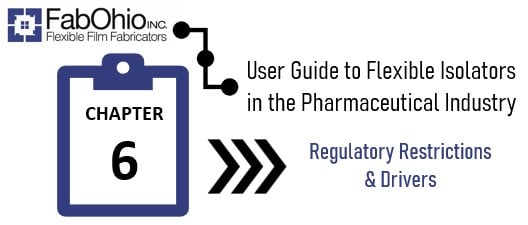
FabOhio Inc. originated serving the highly regulated Nuclear Industry in 1963. When invited to get involved with the Pharmaceutical Industry in 1993, we were well placed to support another heavily regulated industry. Consequently we were able to advance the application of flexible containment in the traditionally glass and steel environment.
At that time, there was autonomy to make changes not directly affecting product. Over time, the Regulatory Agencies changed their auditing approach by introducing Change Control which has stunted evolutionary developments since the turn of the century. We were fortunate to have a time period when we could collaborate with our pharmaceutical partners in testing multiple applications and generating statistically robust ‘rooms within rooms’ using flexible isolation barriers.
The flexible isolator approach was originally considered by the Occupational Health professionals to eliminate worker exposure. Testing rapidly showed this was achieved effectively but the major realization was effective materials containment impacted many areas of Regulatory oversight.
By isolating processes, all surrounding areas remain contaminant free. Furthermore, isolating systems prevents entry of external contaminants. This solves many pre-existing and laborious practices that raised Regulatory audit concerns impacting product integrity.
A high volume of statistical environmental control data in the form of monitoring flexible Isolators during simulated (agency dictated Operational Qualification), and both initial (Performance Qualification) and normal operations (Prolonged Performance Qualification) prove that flexible isolators help to keep a facility free from processing contaminants (down to as low as <0.04 ng/cu.m or <0.04 parts per trillion) meeting the most stringent regulatory criteria to date.
This result benefits many regulations in the US:
- FDA & EMA – product purity
- OSHA – no worker exposures
- EPA – resolves hazmat issues and large reductions in both solid and liquid waste manifests
- CPS – product integrity
In summary, a clean facility is both regulatorily and environmentally healthy and can be cost effectively achieved using flexible isolation barriers.
Written by Brian Ward, PhD, CSci, CChem, FRSC