Pharmaceutical Manufacturing
When it comes to retrofitting older manufacturing facilities that lack the advantage of newer leak-tight equipment, our flexible containment systems provide a convenient, cost-effective solution. They can be safely disposed of and replaced many times over with cumulative costs never approaching a fraction of the cost of a brand new facility.
Any size of enclosure will be capable of handling High Potency, Biotechnology, and sensitizer products, as well as Nanotechnology manufacturing.
Dispensing
Any size of enclosure will be capable of handling High Potency , Biotechnology, and Allergen Drug product and Nanotechnology manufacturing. Our approach to a process is to solve potential issues with worker exposure, fugitive releases (Quality concerns about cross-contamination), and minimizing environmental impact while providing maintenance access. Tight work-spaces have become our specialty.
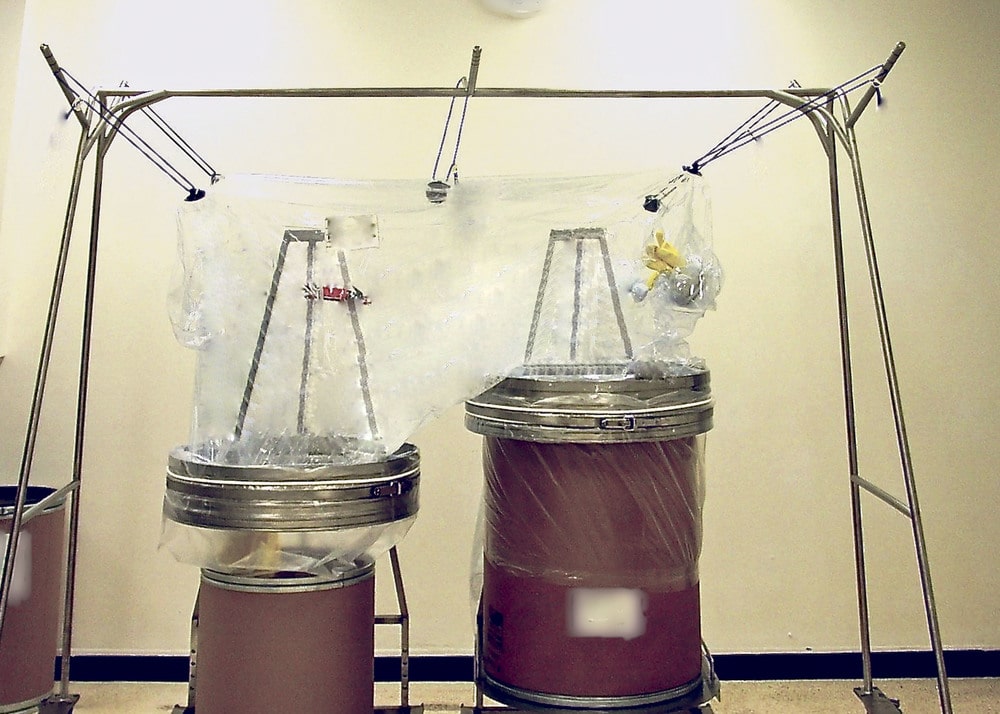
Finishing
Once a finishing process is released from development, it is usually necessary to rapidly implement it in full scale production. Regardless of the age of a facility, achieving contained operations is a challenge due to the nature of the materials handling at every step of manufacture. Instead of purchasing entirely contained equipment which makes access for dosing changes difficult, flexible enclosures form a first line economical solution without the major cleaning costs. Such solutions are light on the pocket - often purchased using a credit card authorization.
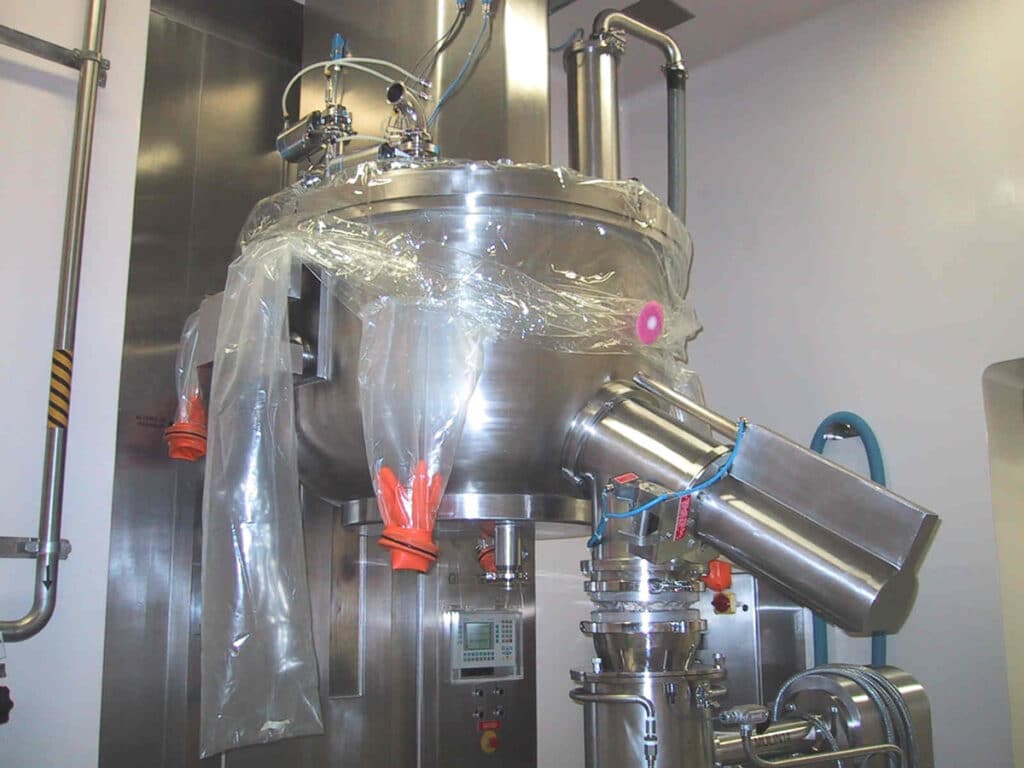
Bulk Processing
Excluding new scratch-built high containment facilities, it comes down to retrofit of existing facilities - many dating back to the 1970's without the advantage of newer leak-tight equipment. Handled properly, this exercise can be $millions less costly, with a time delay of mere weeks, and a virtual elimination of equipment re-validation. Furthermore, entire enclosure system(s) can be disposed of and replaced readily many times over with cumulative costs never approaching a fraction of the cost of a new facility. This also eliminates room cleaning costs, decreasing turnaround time.
Custom Glovebag
System Design
Our team regularly addresses and solves otherwise impossible containment challenges with custom glovebag system design, especially for retrofit where space considerations preclude other approaches.
FabOhio, Inc. is proud to be a partner and originator in creating flexible and disposable containment solutions throughout every aspect of research, development and manufacturing.