Pass-throughs are an integral part of every flexible containment isolator in order to add and remove materials in a contained manner. Both a zippered closure and a cylindrical sleeve can be heat welded onto the sides of a flexible enclosure for isolation of the inner working space from the room environment. In this way materials ingress and egress is controlled to maintain the ‘no cross contamination’ quality mandate.
A simple airlock usually suffices, however a higher level of isolation may be required for specific product working conditions such as moisture free, nano-particle free, and inerting gas environments. This is where the cylindrical sleeve pass-through offers the greatest advantage. Originally developed as a continuous liner for product packaging, requiring extensive cross-contamination and stability testing by the user for compliance with regulatory expectations. A continuous liner used for non-product transfers only requires simple compatibility testing, e.g. solvent compatibility in the same manner that the primary containment enclosure is selected.
The continuous liner has a unique place in today’s regulatory world especially when secured using J-clamps. Because it is attached to the primary containment, the physical environment under which it is sealed is identical with product handling conditions, especially for inerting or moisture constraints. This allows for a liner to be compressed to a convenient size before detachment, and labelling (a label can be printed and attached within the secure loop of a J-clamp). In this way the user can ensure the identity and integrity of the contents when stored and shipped.
Continuous liners are available in several lengths and diameters using the same film used for the containment isolators. They are used to both extend the useful life of an enclosure, and offer a convenient way to retrofit an existing design, as well as providing enhanced isolation performance. When planning to purchase a continuous liner, allowance should be made for adequate length for either normal closures or J-clamps at the ends of a usable space.
The cylinder approach offers several attributes which deliver the greatest level of containment for multiple purposes, I.e. allowing for multiple ‘airlocks’ in the pathway. Short length can be used to introduce materials and tools, but a longer continuous liner delivered on a rigid core providing a means of support would be used for repetitive contained removal of materials, tools, and waste.
Zippered pass-throughs provide a convenient method for atmospheric operations, however their volume will cost operational time when purging is required. Continuous liners can be provided with filtered gas supply and exhaust means which allows the inner volume to be evacuated and filled cost effectively when special atmospheric conditions prevail.
As always, the number and performance quality of airlocks determines the level of isolation achievable. Different procedures can be adopted to circumvent the use of sequential airlocks. One alternative way to achieve a high level of isolation is by using the principles of exponential dilution and exhaust which allows a single purgeable airlock to be used. FabOhio, Inc. developed this approach for our Nano-particle free enclosure. Using an inline J-clamp to isolate the work space and using 2 gas inlets fitted with protective filters, e.g. packed ‘drierite’ or resin columns for moisture control, HEPA Filters for particulate control, or custom nano-particle filters, 2 purge cycles will achieve >98% while a 3 purge cycle will quickly achieve >99.9% displacement of ambient air. An example of this approach is the Nano-particle Glovebag shown on the Videos & Photography section of our website.
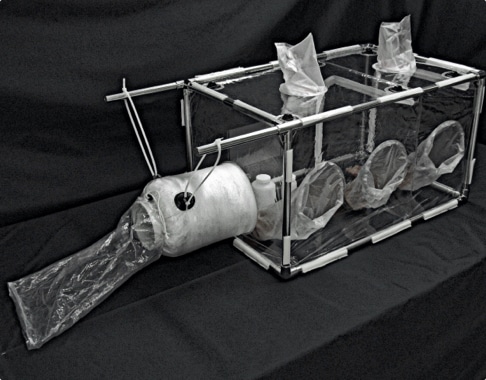
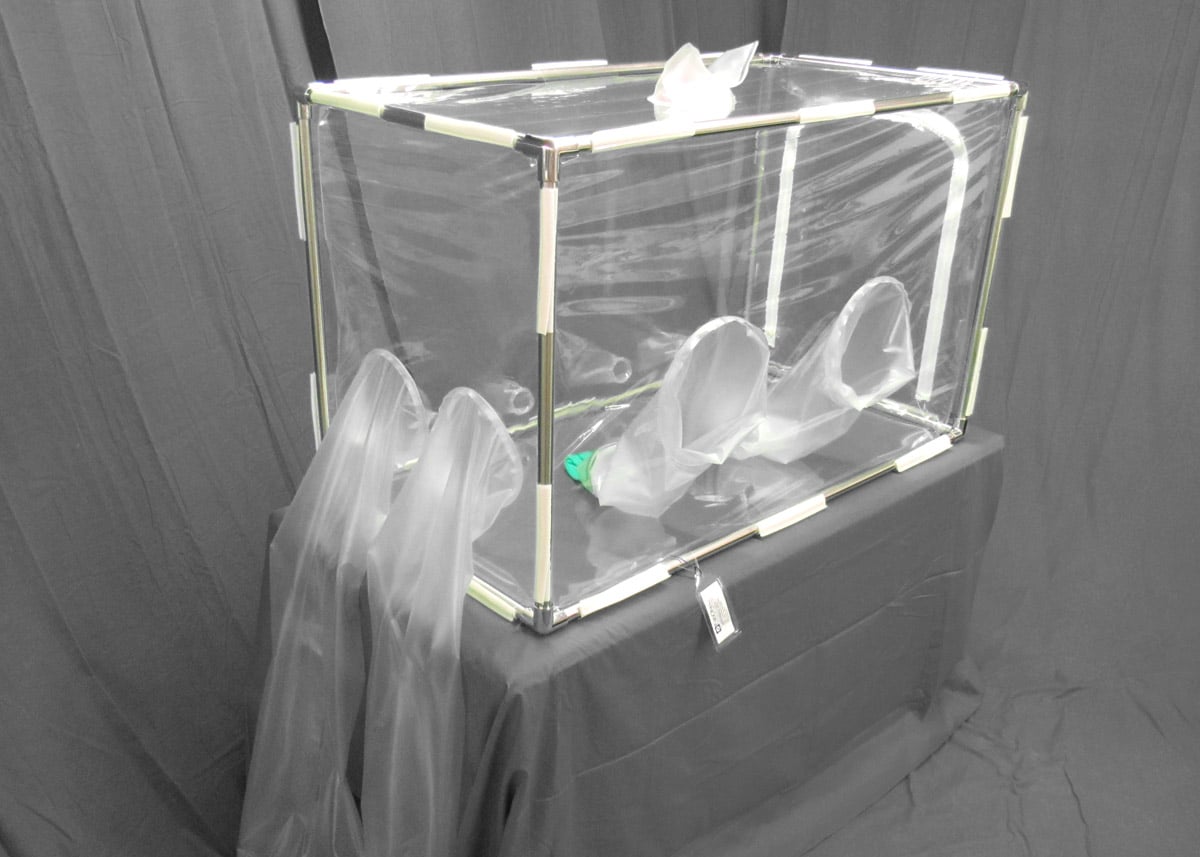
Another advantage of this set-up is the ability to use the purged airlock as additional storage space. In this way tools, sample bottles, etc. will be conditioned during the purge cycles and be accessible to the working space without adding additional footprint. The requirements are for good quality Nylon cable-ties (Nylon 6,6 is the type preferred by Quality), a tie tool for securing, and an electronics size side cutter capable of ‘nibbling’ safely through the Nylon ties.
Flexible isolators are the most cost-effective approaches for equipment and facility retrofits. They can be designed and delivered in short time when supplementing and retrofitting existing hardware, be it placing an enclosure in an existing space such as a walk-in or bench mounted exhaust hood or to enhance an existing containment approach. Size is not a limitation since multiple chamber walk-ins and multiple level isolators having garbing and decontamination capabilities have been constructed and used successfully. Examples of these can be seen on the Videos & Photography section of our website.
Supplementing containment isolators with these capabilities, and in-use emission levels to below 0.04 ng/m3 enhances the user experience in a cost-effective way by substantially reducing Personal Protective Clothing programs, decommissioning, and clean-up costs.
Written by Brian Ward, PhD, CSci, CChem, FRSC